-
whatsapp: +8616696837711
-
wheelim@kelunautoparts.com
-
营业时间 24H
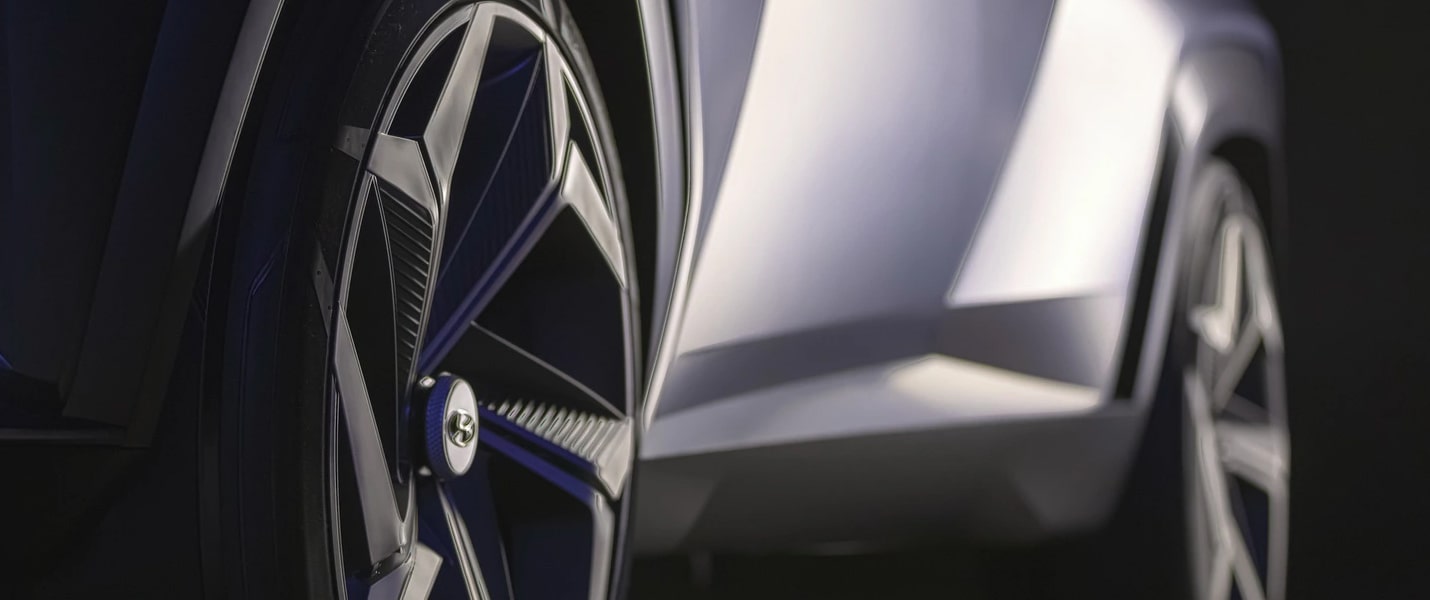
“From design to installation: a full process breakdown of custom wheels”
Custom wheels are a popular way to personalize vehicles, enhance performance, and make a statement. The process of creating and installing custom wheels involves several stages, from initial design to final installation. Here’s a detailed breakdown of the entire process:
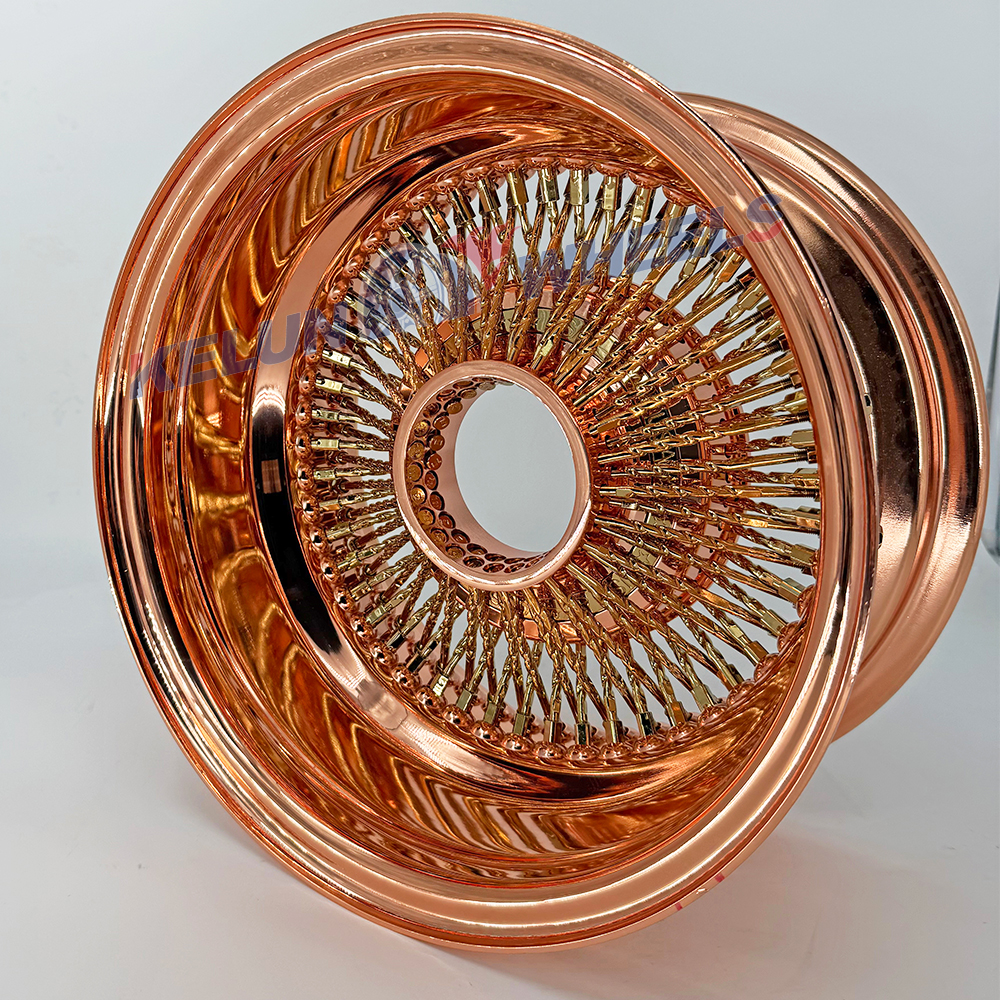
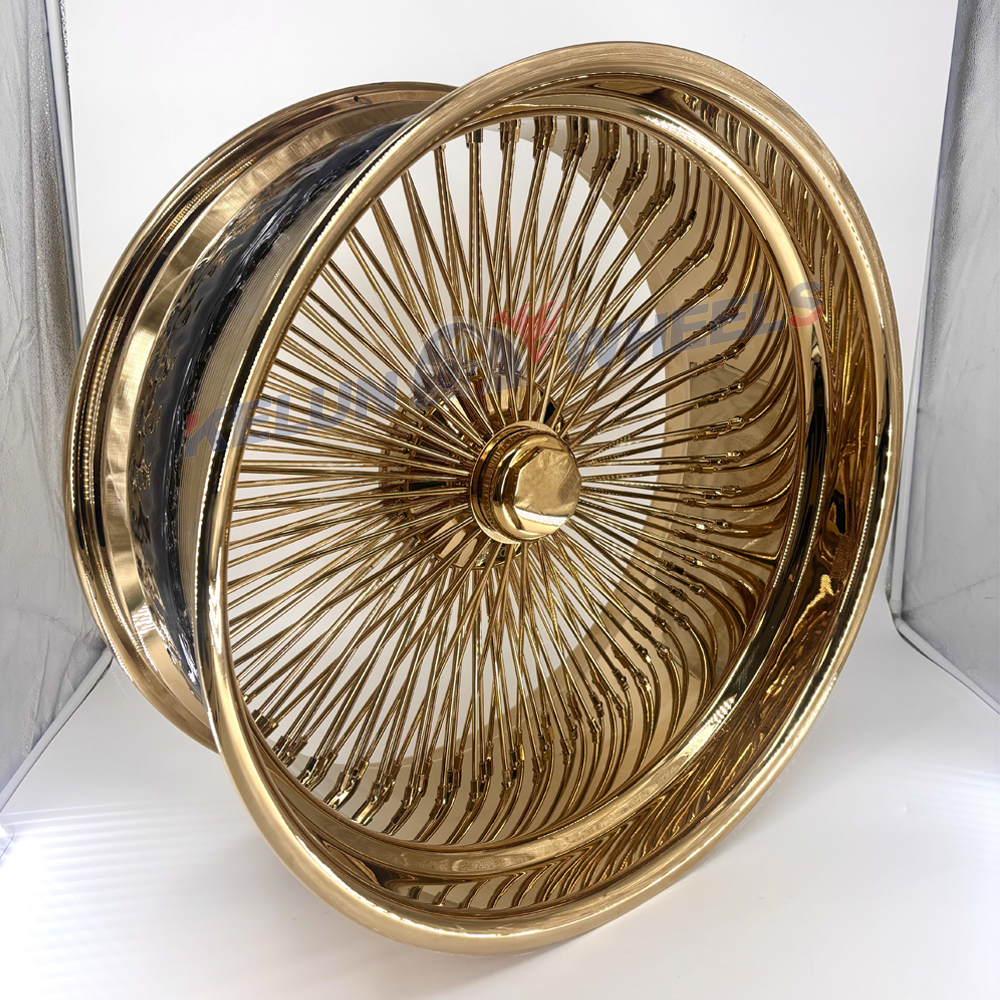
1. Conceptualization and Design
The journey of custom wheels begins with an idea. This stage involves brainstorming and creating a design that aligns with the vehicle owner’s vision and needs.
- Client Consultation:
- Discuss the client’s preferences, including style, size, finish, and performance requirements.
- Consider the vehicle type, driving conditions, and intended use (e.g., street, track, or off-road).
- Design Development:
- Use CAD (Computer-Aided Design) software to create detailed 2D and 3D models of the wheel.
- Experiment with different spoke patterns, offsets, and finishes (e.g., matte, gloss, or chrome).
- Ensure the design meets structural and safety standards.
2. Material Selection
The choice of material impacts the wheel’s strength, weight, and appearance. Common materials include:
- Aluminum Alloy: Lightweight and versatile, ideal for most vehicles.
- Forged Aluminum: Stronger and lighter than cast aluminum, often used for high-performance wheels.
- Steel: Durable and cost-effective, commonly used for off-road or heavy-duty vehicles.
- Carbon Fiber: Ultra-lightweight and high-performance, but expensive.
3. Manufacturing Process
Once the design and materials are finalized, the wheels move into production. The manufacturing process varies depending on the material and design.
- Casting:
- Molten metal is poured into a mold to create the wheel’s shape.
- Suitable for mass production and cost-effective designs.
- Forging:
- A solid piece of metal is heated and pressed into shape under high pressure.
- Results in a stronger and lighter wheel compared to casting.
- CNC Machining:
- A block of metal is precision-cut using CNC machines to achieve the final design.
- Allows for intricate designs and high customization.
- Finishing:
- Apply surface treatments such as polishing, painting, powder coating, or plating.
- Add protective coatings to prevent corrosion and damage.
4. Quality Control and Testing
Before the wheels are deemed ready for use, they undergo rigorous testing to ensure safety and performance.
- Structural Integrity Tests:
- Check for cracks, weaknesses, or defects using X-rays or ultrasound.
- Load Testing:
- Simulate heavy loads to ensure the wheels can withstand real-world conditions.
- Impact Testing:
- Assess durability by subjecting the wheels to sudden impacts.
- Balancing and Runout Testing:
- Ensure the wheels are perfectly balanced and round for smooth operation.
5. Customization and Personalization
Custom wheels often include unique touches to reflect the owner’s style.
- Custom Colors and Finishes:
- Offer a wide range of colors, textures, and effects (e.g., two-tone, brushed, or chrome).
- Engraving or Etching:
- Add logos, patterns, or text for a personalized look.
- Custom Center Caps:
- Design center caps that match the wheel’s aesthetic.
6. Installation
Once the wheels are ready, they are installed on the vehicle. Proper installation is crucial for safety and performance.
- Tire Mounting:
- Select tires that match the wheel size and vehicle requirements.
- Use professional equipment to mount and balance the tires.
- Alignment:
- Ensure the wheels are properly aligned to prevent uneven wear and improve handling.
- Torque Specifications:
- Tighten lug nuts to the manufacturer’s recommended torque settings.
- Final Inspection:
- Check for proper fitment, clearance, and overall appearance.
7. Maintenance and Care
After installation, maintaining custom wheels is essential to preserve their appearance and functionality.
- Regular Cleaning:
- Use appropriate cleaning products to remove dirt, brake dust, and grime.
- Protective Coatings:
- Apply sealants or ceramic coatings to protect against corrosion and UV damage.
- Inspection:
- Periodically check for damage, cracks, or bends, especially after driving on rough terrain.
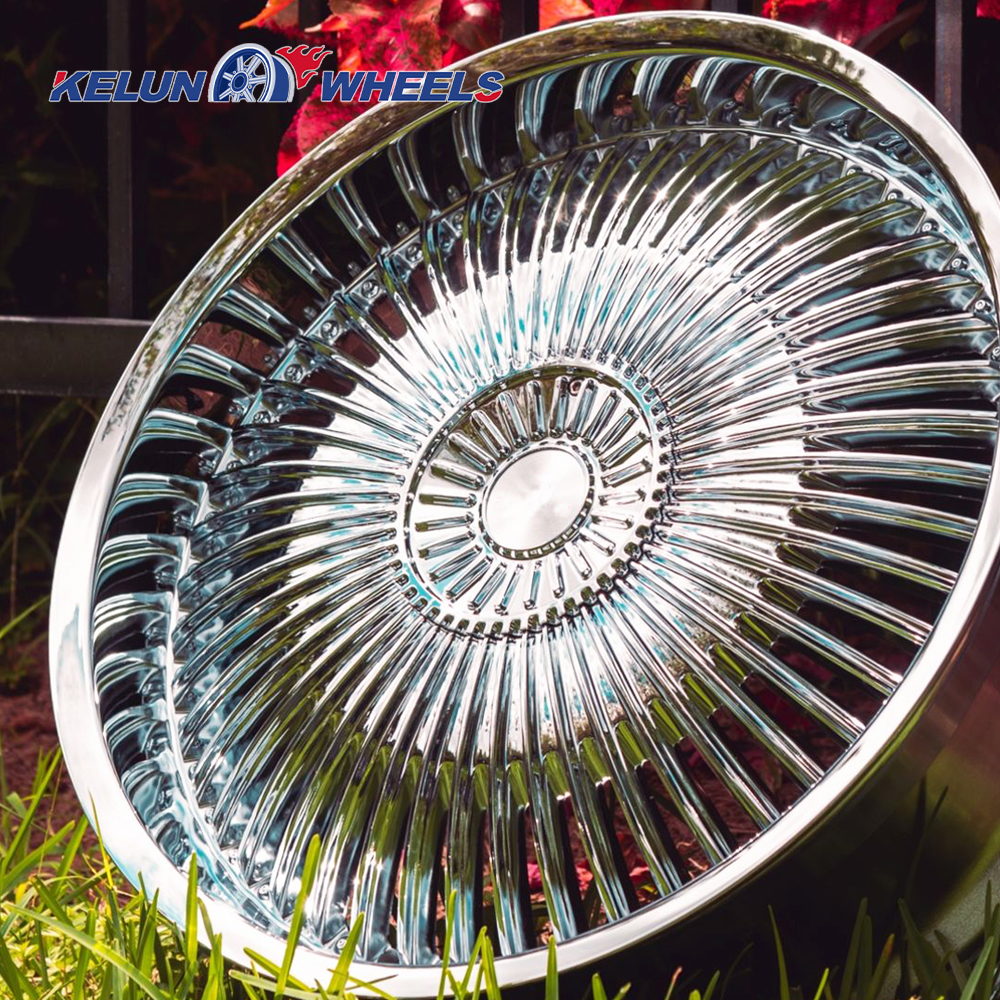
The process of creating and installing custom wheels is a blend of artistry, engineering, and precision. From the initial design to the final installation, each step requires careful attention to detail to ensure the wheels meet the client’s expectations and perform flawlessly on the road. Whether for aesthetics or performance, custom wheels are a testament to the marriage of form and function in automotive design.
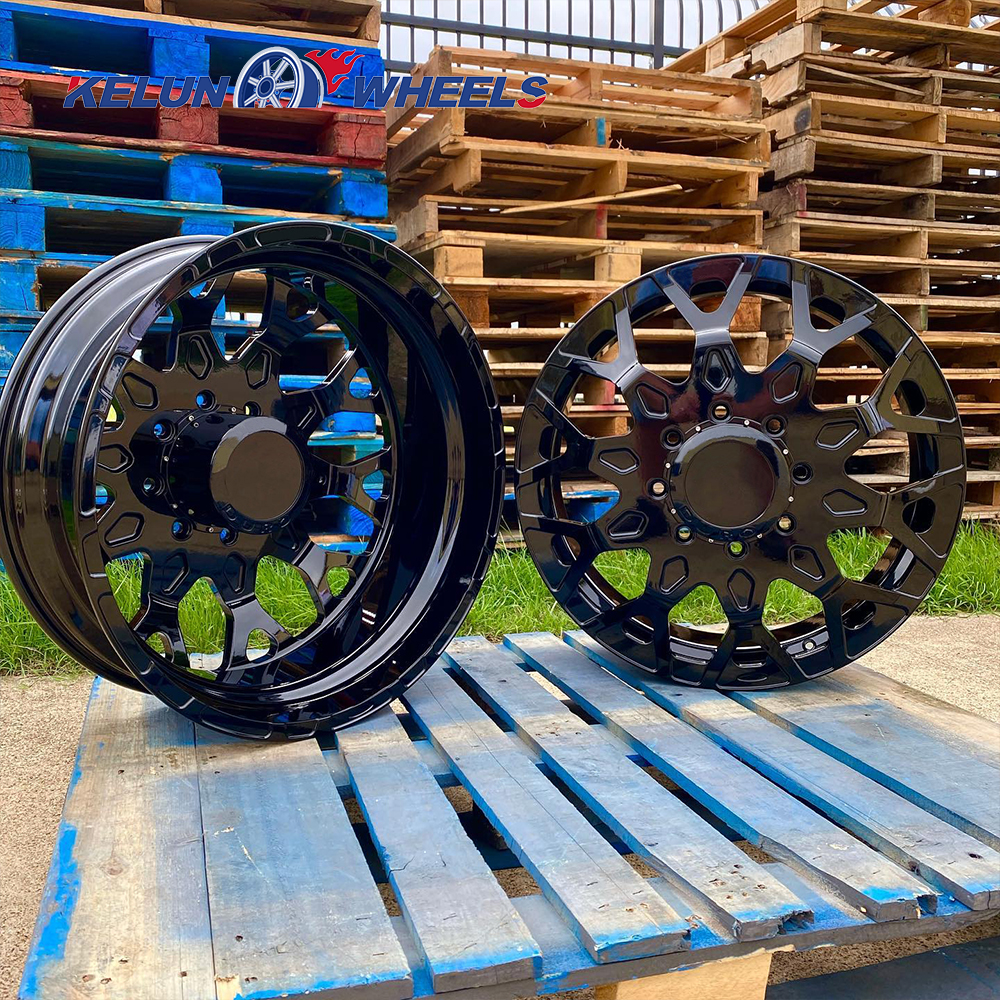
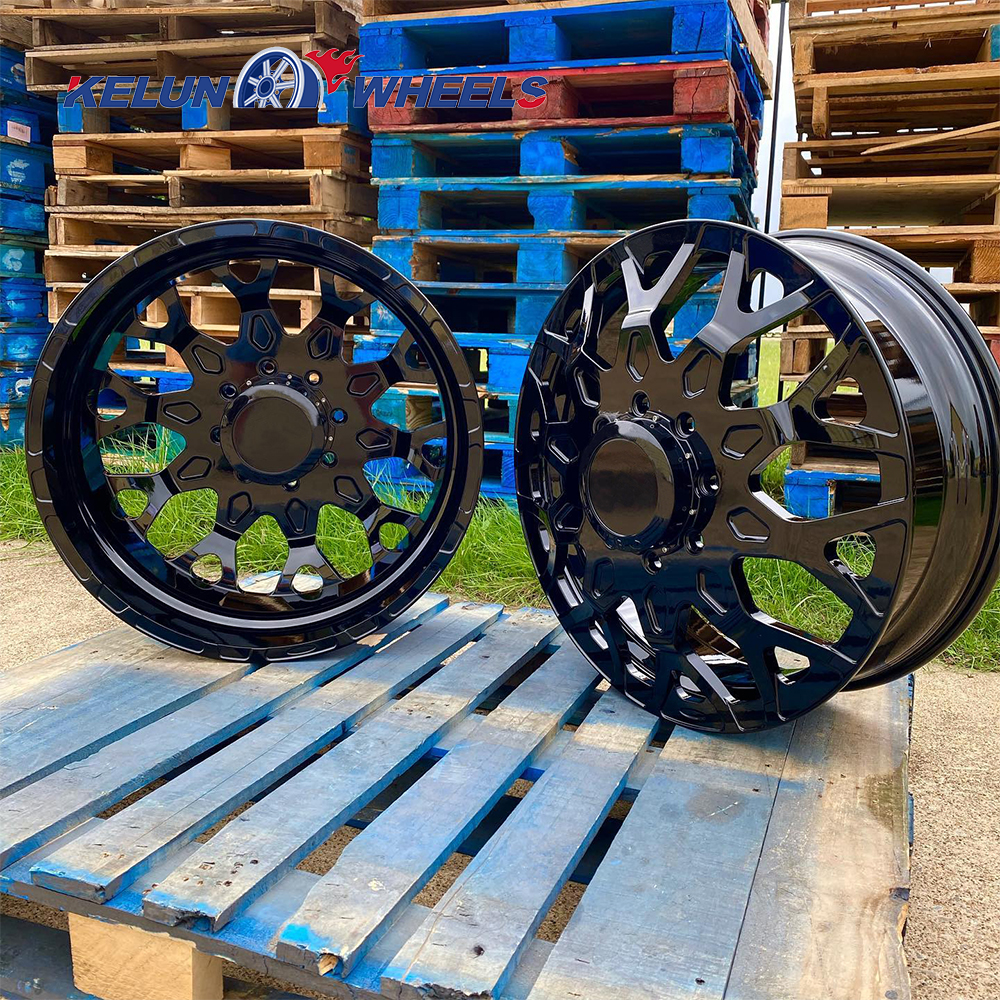